5 September 2024
What are the consequences of PPE non-compliance?
Personal protective equipment (PPE) or protective workwear is absolutely vital for anyone employed in industries where potential hazards or contamination concerns are commonly found. PPE can include hard hats, safety goggles, chemical-resistant clothing, anti-static garments, high-visibility attire, welding protection garments, gloves, steel-toe boots, and much more. You can find PPE across a wide range of industries, including healthcare, construction, welding, manufacturing, food production, warehousing, and fire and rescue services.
According to The Personal Protective Equipment at Work Regulations 1992, employers in the UK must provide PPE to any and all employees who are exposed to health and safety risks at work, such as the risk of falling goods in a warehouse or molten metal in a welding shop. However, what can you do if your employees choose not to wear their PPE, or if they repeatedly wear it incorrectly?
Here at alsico, we’re well aware of the worrying trend of PPE non-compliance. Below, we’ve put together a helpful guide to warn you of the risks involved, and to show you how to combat it in the workplace.
Why is PPE important in the workplace?
PPE helps to prevent injuries and accidents in the workplace, ensuring wearer protection whilst also reducing the risk of legal action from employees. PPE is required in industries and roles where employees are exposed to potential health and safety risks, such as the risk of burns, cuts, impacts and exposure to chemical irritants in sectors like manufacturing and construction. Plus, PPE workwear is also used in sectors where employees need to reduce the risk of contamination and be protected against bacteria and viruses, such as the healthcare and food processing industries.

what are the risks associated with not wearing PPE correctly?
Without PPE, employees wouldn’t be able to work in the industries mentioned above without being at serious risk of a wide range of accidents, injuries and diseases. In addition, employers would constantly face legal action from injured ex-employees, and along with the reduced productivity caused by workplace accidents, this would be financially catastrophic for businesses and entire sectors of the economy.
Not only is not wearing any PPE extremely dangerous, but wearing it incorrectly is also a huge problem. Even if an employee is wearing most of their PPE, they could still become injured on exposed parts of their body. For example, if a construction worker took off their hard hat even for a few minutes whilst on-site, it could only take a moment for a tragic accident to occur. Ill-fitting PPE is also problematic, as workwear that’s too large could easily get caught on machinery and cause injuries, or too-tight clothing could restrict movement dangerously.
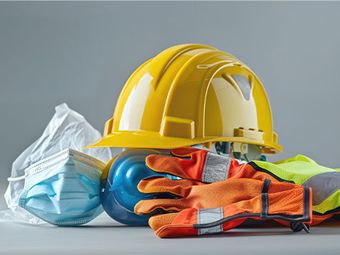
So what exactly could these risks include for everyone involved? Here are just a few examples of real risks that employees and employers could face as a result of PPE non-compliance:
Risks for employees
Healthcare workers could be exposed to harmful bacteria and viruses if they don’t have the proper PPE that minimises the risk of cross-contamination in healthcare environments, whilst also ensuring unrestricted movement. Some healthcare workers may also need masks, respirators, aprons and eye protection depending on their role.
Without welding protection garments, such as those supplied by alsico, welders are at serious risk of severe burns and other injuries.
Arc flash injuries can cause burns, blast injuries, hearing damage and the inhalation of toxic smoke for electrical workers who don’t have the right PPE. Arc flash protective workwear uses fabrics that limit the spread of flames and protects against the risk of second and third degree burns, whilst also providing plenty of stretch for user comfort and mobility.
Anti-static/ESD garments are also essential for electrical workers or workers in any industry where electrostatic discharge presents a threat.
Without high-visibility workwear, employees on industrial and construction sites are at risk of being injured by machinery and vehicles if the operators are unable to see them clearly.
A lack of adequate hand protection and chemical-resistant clothing in certain environments will increase the risk of cuts and exposure to harmful substances in the workplace, leading to various diseases, disabilities, skin irritation, lacerations, infections, burns and long-term issues like chronic illness, cancer, scarring and disfigurement.
- Workers on construction sites and in factories, welding shops and warehouses must have protective headgear to prevent serious head injuries from falling objects. Foot injuries can also be very common in these settings due to slippery surfaces, falling objects, and collisions with sharp objects, which is why steel-toe boots and other types of safety boots are needed to prevent serious injuries and long-term mobility issues.
Risks for employers
Since employers are responsible for providing PPE and ensuring it’s worn when needed, PPE non-compliance can lead to an increase in legal action from employees who have been injured in the workplace. This can generate colossal legal expenses for employers.
In addition to legal expenses, businesses will face increased operational costs due to reduced productivity caused by workplace accidents and injuries.
In turn, reduced productivity caused by PPE non-compliance can then lead to projects not being completed on time, resulting in additional costs, potential penalties, and lost business.
The Health and Safety Executive (HSE), the national health and safety regulator in the UK, can issue hefty fines to companies that don’t ensure PPE compliance. In cases where people’s lives are endangered or lost, bosses can face even larger fines and imprisonment.
An increase in accidents and legal problems from PPE non-compliance may damage your business’s reputation, creating the image that you don’t care about employee safety.
- Workers on construction sites and in factories, welding shops and warehouses must have protective headgear to prevent serious head injuries from falling objects. Foot injuries can also be very common in these settings due to slippery surfaces, falling objects, and collisions with sharp objects, which is why steel-toe boots and other types of safety boots are needed to prevent serious injuries and long-term mobility issues.
Long-term risks for the company
Your business’s damaged reputation due to workplace accidents could lead to difficulties hiring and retaining employees, missed business opportunities, and decreased profits in the long run.
- A lack of proper PPE provision, training and discipline will breed a culture of PPE non-compliance, further increasing the risk of accidents and injuries over time
Who is responsible for providing PPE?
The employer is responsible for providing PPE for all workers who may be exposed to health and safety risks in the workplace, as explained in The Personal Protective Equipment at Work Regulations 1992. If current PPE workwear is incomplete, ill-fitting, or unsuitable for any reason (e.g. religious or health reasons), it’s the employer’s responsibility to provide the right PPE for that individual employee by accommodating these needs. Until the right PPE is provided, workers should be temporarily moved to a different role that doesn’t involve health and safety risks.
However, this can cause problems when employees repeatedly refuse to wear their PPE correctly, even when the right workwear has been provided. There may also be issues if there’s no alternative work available for an employee who can’t wear PPE, even after adjustments have been attempted. Ultimately, health and safety is one of the most important responsibilities for employers, so if an employee won’t or can’t wear their PPE in hazardous environments, the employer is within their rights to dismiss them rather than allow this person to put themselves in danger.
Who is responsible for ensuring PPE compliance?
In addition to being responsible for providing PPE, employers are also responsible for ensuring that it’s worn correctly and consistently by employees. For instance, in the examples described above, employers are required to make suitable adjustments to an individual employee’s PPE if it’s not right for them, and they must provide alternative work if possible until the PPE is provided.
However, this can cause problems when employees repeatedly refuse to wear their PPE correctly, even when the right workwear has been provided. There may also be issues if there’s no alternative work available for an employee who can’t wear PPE, even after adjustments have been attempted. Ultimately, health and safety is one of the most important responsibilities for employers, so if an employee won’t or can’t wear their PPE in hazardous environments, the employer is within their rights to dismiss them rather than allow this person to put themselves in danger.
how to improve PPE compliance in the workplace
Now you know the importance of PPE compliance, how can you ensure that PPE is worn consistently and correctly in your workplace? Here are our top tips:
1. Provide correct and properly fitting PPE for all employees
All employees need the right PPE for their job to ensure health and safety. However, even if a worker has the right equipment, it could be inadequate at protecting them or even put them at risk if it doesn’t fit correctly. This issue is particularly prevalent among female employees, who often deal with PPE workwear that is too large and ill-fitting, causing trips, falls, entanglements in machinery, and a range of other accidents and injuries. This has been highlighted by authors and campaigners, like Invisible Women author Caroline Criado Perez, who reported that “while PPE is usually marketed as gender-neutral, the vast majority has in fact been designed around a male body, and therefore neither fits nor protects women.”
Therefore, to ensure workplace safety, employers must provide correct and properly fitting PPE for all employees, including PPE designed for all bodies and a wide range of heights and body shapes. Here at alsico, we recognise the vital importance of PPE that fits everyone, which is why we supply PPE workwear designed for male and female bodies, with extensive size and height ranges to suit all workers. We don’t believe in a ‘one-size-fits-all’ approach, which is why we also design and supply bespoke PPE workwear and uniforms for our customers to suit any environment, application or body type.
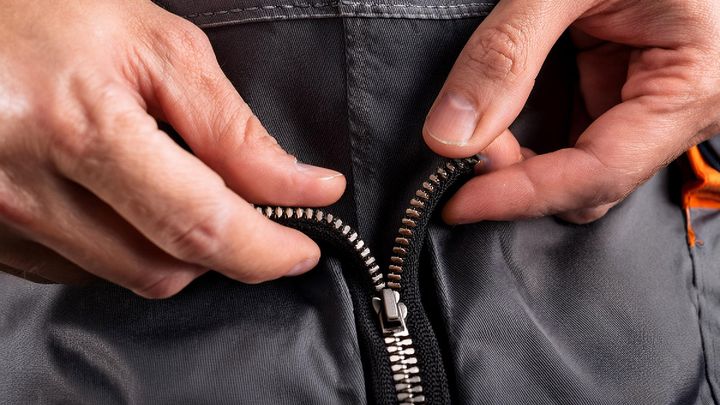
accommodate medical conditions and religious beliefs
Employers are responsible for ensuring PPE compliance, so wherever possible, they must try to make reasonable adjustments to PPE so that employees with specific needs can wear it properly. If an employee isn't currently wearing their PPE correctly, it’s important to listen to their concerns so that a solution can be found.
For example, if an employee has a skin condition like eczema or psoriasis that makes it difficult to wear certain fabrics or clothing styles, could an alternative item or material be found? As long as the new PPE doesn’t decrease their safety compared to other employees, this would be a reasonable adjustment that you have the responsibility to make.
Remember to accommodate various religious beliefs in the workplace too. For instance, Hindus and Jains may object to wearing cow leather, and Muslims may object to wearing products made from pig skin, so alternative materials should be found if requested. Plus, turban-wearing Sikhs can choose not to wear protective headgear, according to UK law.
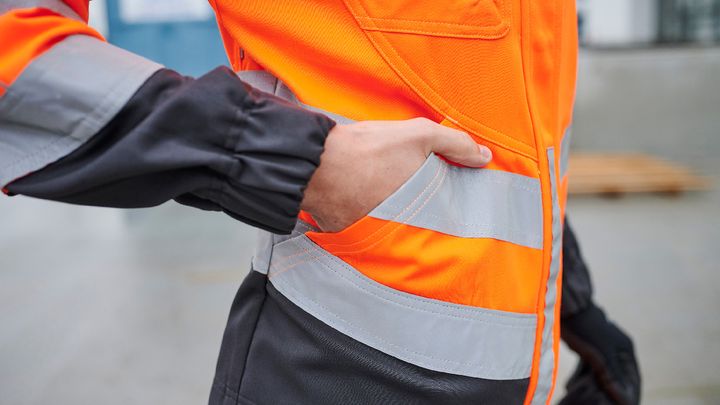
ask for employees’ input
Often, employees will feel happier following processes at work if they’re involved in decision-making, as this gives them a greater sense of control and agency over their own careers. If your employees currently aren’t wearing PPE correctly, encourage them to share their opinions with you and make suggestions about what kinds of PPE they would be happy to wear. You may discover that your employees were simply unhappy with the poor materials and sizing options provided by your current workwear supplier, and in this case, you can look into more suitable choices together.
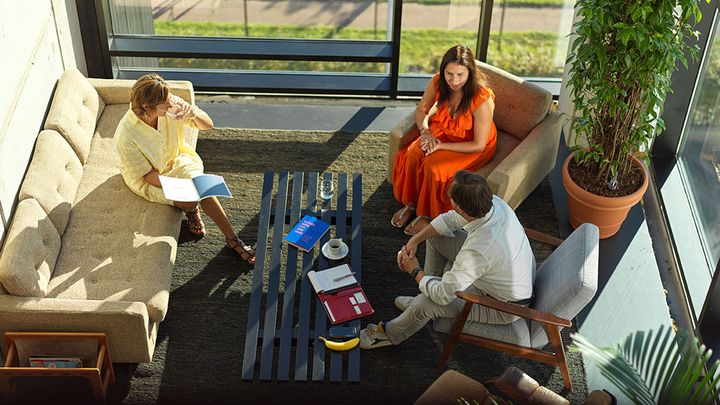
4. provide PPE training
PPE non-compliance is often caused by a lack of understanding of the true risks associated with not wearing PPE correctly. Your employees may not be fully aware of the dangers they could face by not following PPE policy, and may think you’re just trying to enforce meaningless uniform rules.
To ensure that everyone in your team fully understands the importance of PPE, you should provide health & safety and PPE training sessions that educate employees on potential dangers in their workplace, and on why each piece of PPE is essential for their health and safety. There are plenty of educational videos and other resources online that explain why wearing the right PPE is vital for each employee and for creating a safety-conscious company culture. Hearing first-hand accounts of workplace injuries from real people will be particularly impactful for employees who currently aren’t complying with PPE guidelines.
Training should be provided during each onboarding process and at regular intervals throughout everyone’s employment. This will make sure that the importance of PPE is constantly emphasised and remains at the forefront of people’s minds.
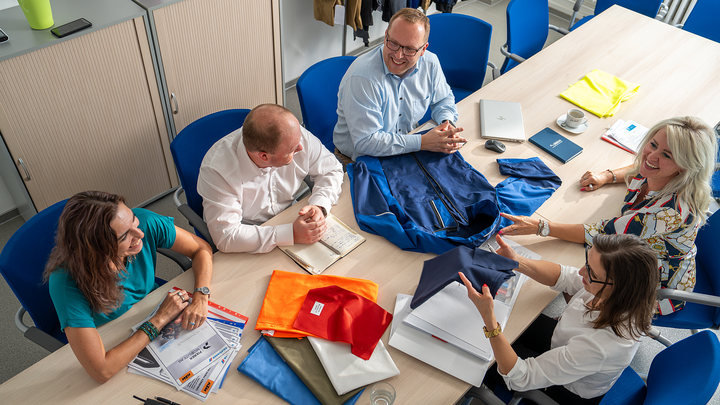
5. Enforce PPE compliance with disciplinary action
If regular company training and listening to individual concerns still isn’t producing the desired effect, it’s necessary to enforce compliance through employment contracts, employee handbooks and disciplinary procedures. Not only is PPE vital for protecting workers’ health and safety, but it’s also crucial for protecting the business against costly legal action resulting from workplace injury claims, so you need to protect yourself legally.
Each contract and handbook should have a dedicated section on PPE if this is relevant to your business, stating PPE rules and your expectations regarding everyone’s compliance. For example, you can state that PPE must be worn when required and looked after according to PPE training, and that refusal to wear correct PPE can be treated as gross misconduct and result in dismissal. This doesn’t absolve the company from its responsibility to provide the right PPE and ensure it’s worn in the first place, but it can make the dismissal process easier and potentially prevent future legal action for unfair dismissal by making expectations clear.
Finally, make sure you have a clear disciplinary procedure in place to deal with PPE non-compliance. Matters should be handled in a more informal manner at first if possible, by asking employees what can be done to make it easier for them to wear their PPE correctly. If this fails, there should be a set number of warnings before dismissal, or a clause that defines extreme examples of non-compliance (e.g. refusal to wear any PPE on a dangerous site) as gross misconduct and grounds for immediate dismissal.
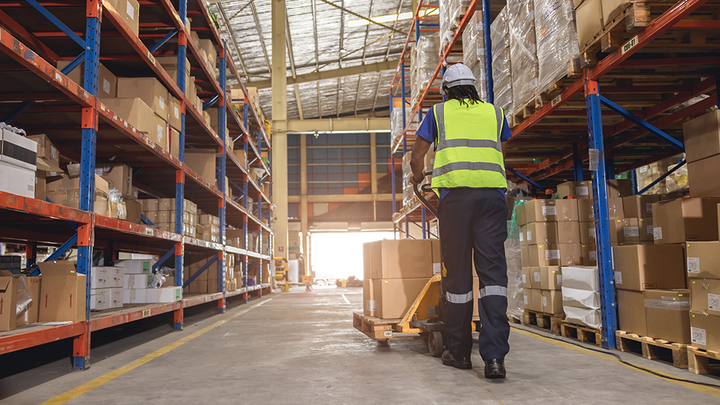
6. Be a good example
Change should start from the top down. If you want to make sure employees are wearing their PPE workwear correctly, high-level employees should lead by example and always wear the correct gear on-site. Employees are less likely to comply if they feel like rules aren’t applied fairly.
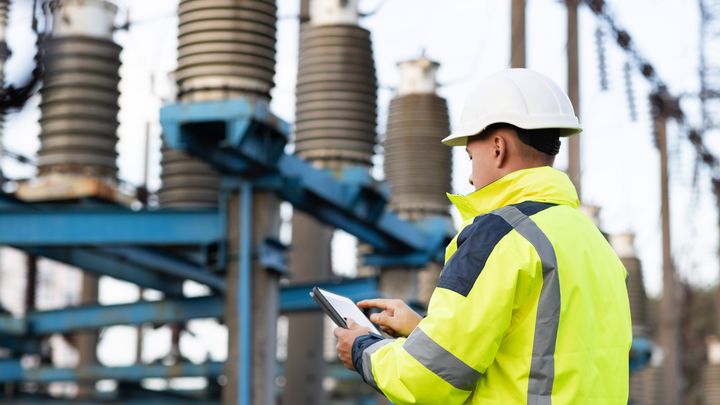
Alsico was founded on the principle that all employees should have high-quality protective clothing in the workplace. Discover PPE, protective workwear, and uniforms for a wide range of industries and applications on the alsico website, including Healthcare, Wearer Protection, Contamination Control, Emergency Response and more. Contact us today to discuss your supply needs or find out more about our bespoke design service for uniquely tailored solutions.
contact us