6 November 2024
Common welding injuries and how to prevent them
Welding is a crucial production process in many industries. And whilst it has many uses, it can also expose workers to a range of potential hazards. From intense heat and flames to toxic fumes and flying sparks, welders face numerous risks that can lead to serious injuries if proper safety measures are not taken.
In this guide, we’ll look into what common welding injuries may occur if the right preventative measures aren’t in place, and how proper welding PPE and other protocols can help to mitigate welding injuries.
why can welding cause injury?
Welding involves working with tools that create high temperatures, intense ultraviolet and infrared radiation, and molten metal - all of which can cause severe burn injuries to the skin and eyes. Plus, welders are exposed to harmful fumes and gases, such as carbon monoxide, ozone, and metal fumes, which can lead to respiratory problems and long-term health issues if not properly managed.
Other common welding hazards include (which we’ll dive into further on):
- Noise-induced hearing loss (NIHS)
- Musculoskeletal disorders from awkward postures and repetitive motions
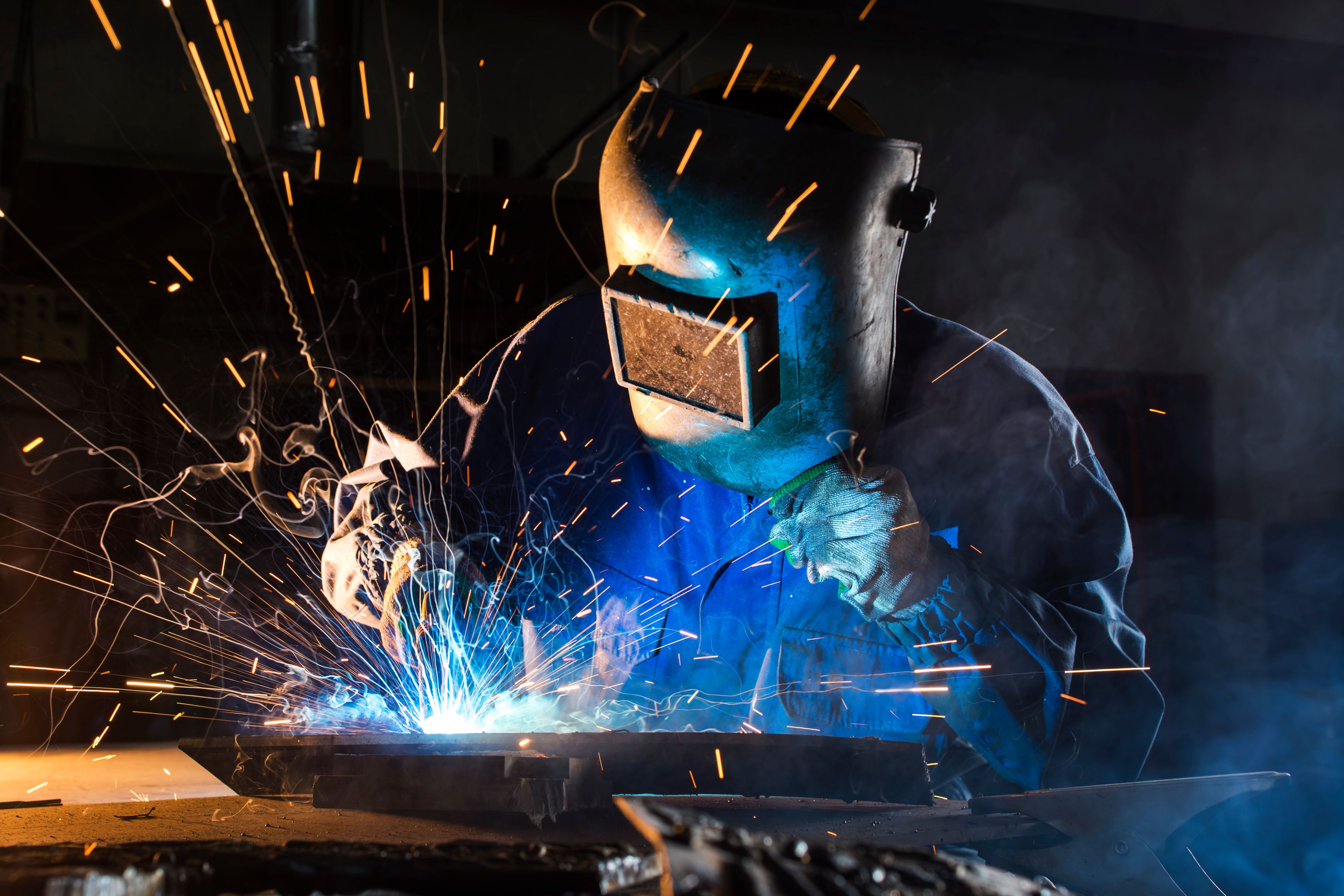
the most common welding injuries
Below are some of the most common welding injuries that could happen on the job:
1. burns
Burn injuries are among the most common faced by welders, due to exposure to intense heat, flames, sparks, or molten metal during the welding process. There are three main types of burn injuries that welders should be aware of:
- Thermal Burns. Thermal burns are caused by direct contact with hot surfaces, flames, or radiant heat. These burns can range from minor to severe, depending on the temperature and duration of exposure. Thermal burns can occur on any exposed skin, particularly the hands, arms, and face.
- Electrical Burns. Welders working with electric arc welding processes are at risk of electrical burns. These burns can occur when the welder's body becomes part of the electrical circuit, causing severe tissue damage and internal injuries.
- Chemical Burns. Certain welding processes involve the use of chemicals, such as fluxes or cleaning agents, which can cause chemical burns if they come into contact with the skin or eyes.
Prevention
To prevent burn injuries, welders should always wear fire-resistant PPE and a welding helmet with a proper filter lens (PPE). Besides following proper welding techniques, it’s also important to maintain a safe distance from the arc or flame and ensure adequate ventilation to reduce the risk of exposure to hot surfaces or molten metal.
Your employer is responsible for providing PPE - so if you believe yours to be defective or you’re unsure of where to source it, they will be your first port of call. Alternatively, alsico are manufacturers and suppliers of heat, flame and welding PPE - so if you’re an employer - contact us to find out more.
2. eye injuries
One of the most common and serious hazards for welders is a flash welding eye injury from exposure to intense ultraviolet (UV) and infrared radiation produced by the welding arc. This radiation can cause painful inflammation of the cornea, permanent eye damage and vision impairment if not properly protected.
- “Arc eye” (welder's flash). Arc eye, also known as welder's flash or flash burn, is a painful eye condition caused by exposure to the intense UV radiation emitted by the welding arc. Symptoms include a gritty sensation, excessive tearing, light sensitivity, and the feeling of having something in the eye. These symptoms typically appear several hours after exposure and can last for days, severely impacting vision and productivity.
- UV radiation-based issues. Prolonged or repeated exposure to UV radiation from welding arcs can lead to more serious eye injuries. It can cause the formation of cataracts, which cloud the eye's natural lens and impair vision. UV exposure can cause growths on the eye called pterygium, which can eventually obstruct vision if left untreated.
Prevention
To prevent eye injuries, welders must wear proper eye protection designed specifically for welding operations. Welding helmets or goggles with appropriate shade lenses that filter out harmful UV and infrared radiation are essential. These lenses should be inspected regularly and replaced if damaged or if the lens tint has faded.
Welders should also be trained on the proper use and maintenance of their eye protection equipment. Installing protective screens or curtains around welding areas can help prevent accidental exposure to other employees.
3. respiratory issues
Welding operations can generate various airborne contaminants, including fumes, gases, and metal particulates, posing significant respiratory hazards to welders. This can lead to acute and chronic respiratory diseases if proper precautions are not taken.
- Fumes. Welding fumes are a complex mixture of metal oxides and other compounds produced during the welding process. These fumes can contain toxic substances like hexavalent chromium, manganese, nickel, and lead, depending on the base metal and welding consumables used. Exposure to welding fumes can cause metal fume fever, a flu-like condition with symptoms such as fever, chills, nausea, and shortness of breath.
- Gases. Welding can also produce harmful gases, including carbon monoxide, ozone, and nitrogen oxides. Carbon monoxide is a colourless, odourless gas that can cause headaches, dizziness, and even death in high concentrations. Ozone, a byproduct of the welding arc, can irritate the eyes, nose, and throat, and prolonged exposure can lead to respiratory problems. Nitrogen oxides, generated during certain welding processes, can cause symptoms such as coughing, shortness of breath, and lung irritation.
- Metal particulates. Welding operations can generate metal particulates, such as iron, aluminium, and stainless steel, which can be inhaled and accumulate in the lungs. Long-term exposure to these particulates can lead to lung diseases like pneumoconiosis, a condition characterised by scarring and stiffening of the lung tissue.
prevention
To protect yourself or your employees from respiratory hazards, it is essential to use and/or supply appropriate respiratory protection equipment. Depending on the welding process and the level of exposure, welders may need to wear air-purifying respirators with particulate filters or supplied air respirators (such as FFP3 disposable mask or half-mask with P3 filter). Adequate ventilation, such as local exhaust ventilation systems, can also help reduce exposure to welding fumes and gases.
Your building’s local exhaust ventilation system (LEV) will also need to be in full working order and fully compliant to reduce welding fumes in the surrounding work environment.
4. NIHL
Welding can be noisy, often exceeding safe exposure limits. The intense noise generated by welding equipment - such as arc welding machines, grinders, and other tools - can cause NIHL over time. The main cause of NIHL in welding is prolonged exposure to high decibel levels of noise - typically around 85 dB and above. It’s a permanent and irreversible condition that can significantly impact a welder's quality of life and ability to work safely.
NIHL can have severe consequences for welders, including:
- Temporary or permanent hearing loss
- Tinnitus (ringing, buzzing, or whistling in the ears)
- Difficulty understanding speech, especially in noisy environments
- Increased risk of accidents due to impaired communication and situational awareness
prevention
Using ear defenders is imperative when welding and to prevent the risk of NIHL. Here are some other ways you can reduce the risks:
- Earplugs. Disposable earplugs or earmuffs designed for high-noise environments can effectively reduce noise exposure. Ensure they are properly fitted, can protect against the right decibel amount and replaced regularly.
- Consider welding booths. Welding booths or enclosures with sound-absorbing materials can significantly reduce noise levels at the source.
- Implement frequent welding shift rotations. Work rotation schedules to limit individual exposure time, and provide quiet areas for breaks and rest periods.
5. musculoskeletal disorders
Welding work often involves sitting and bending your neck and/or back into awkward postures, repetitive motions, and heavy lifting, which can lead to musculoskeletal disorders (MSDs) such as back pain, neck strain, carpal tunnel syndrome, and tendonitis. These injuries can be debilitating and may require time off work for recovery.
Unfortunately, ergonomic risks in welding arise from the nature of the work itself. Welders frequently have to bend, twist, and reach into confined spaces, putting strain on their backs, shoulders, and necks. Holding welding guns or torches for extended periods can cause hand, wrist, and arm fatigue. Plus, welders may need to lift and manoeuvre heavy materials, increasing the risk of back injuries.
prevention
Hope isn’t all lost, and there are lots of ways to prevent MSDs. Including:
- Providing adjustable workstations and welding booths that allow for comfortable postures and minimise reaching and bending.
- Using ergonomic tools and equipment, such as counterbalanced welding guns or torches, to reduce hand and arm strain.
- Implementing job rotation and frequent breaks to alleviate repetitive stress and fatigue.
- Training welders on proper lifting techniques and using mechanical aids for heavy loads.
- Encouraging stretching and warm-up exercises before, during (shifts) and after work.
Employers should also conduct ergonomic assessments to identify and mitigate specific MSD risks in their welding operations. Regular monitoring and adjustments to work practices can help prevent musculoskeletal injuries and ensure a safer and more productive welding workforce.
what PPE should welders wear?
PPE is non-negotiable for welders, particularly due to the nature of the work involving dangerous materials, molten metals, bright light and the rest. Here are the PPE items you must supply to your welding employees:
1. welding helmets
Welding helmets shield a welder's face and eyes, from bright light, heat, and sparks that welding creates. These helmets generally have a special visor with a tinted lens to block harmful UV and infrared rays. New helmets on the market often have an auto-darkening filter (ADF), which changes how dark the lens is based on how bright the welding arc is. This lets welders see when they're not welding but still protects them when they are. This design helps to prevent eye problems, like "arc eye," to make welding more precise and safe.
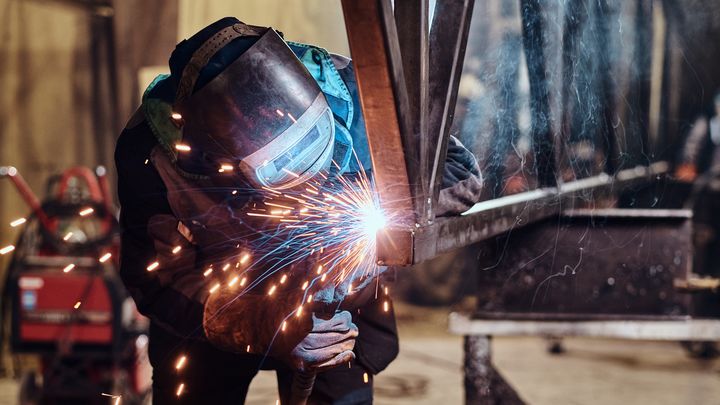
2. protective clothing
Wearer protection is paramount for welders. They must wear flame-resistant clothing made from materials like leather, wool, or treated cotton (like our flame retardant cotton). These garments protect the welder's body from sparks, molten metal splashes, and radiant heat. Protective welding clothing will typically include jackets, aprons, leggings, and spats, covering as much of the body as possible.
Our coveralls here at alsico are EN ISO 11611:2015 Class 1 A1 and EN ISO 11612:2015 A1 B1 C1 F1 - the standard required for PPE that protects the wearer's body from heat and/or flame.
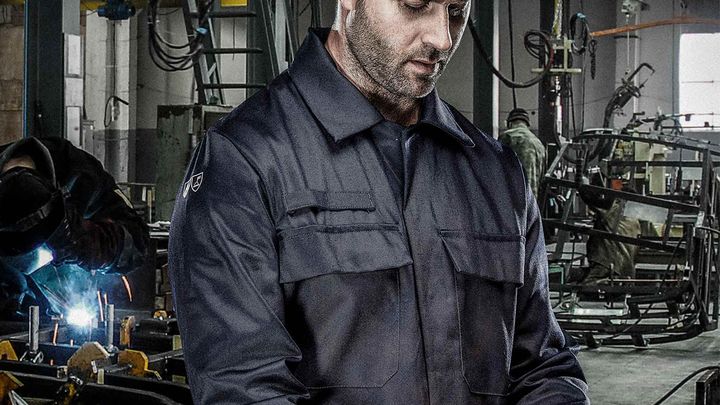
3. welding gloves
Molten metal can be protected against with welding gloves; they’re also essential for protecting the hands from burns, cuts, and abrasions. These gloves are made from heat-resistant materials like leather or enhanced fabrics, designed to withstand high temperatures and molten metal splashes. Some gloves also offer additional protection against sharp objects and electrical hazards.
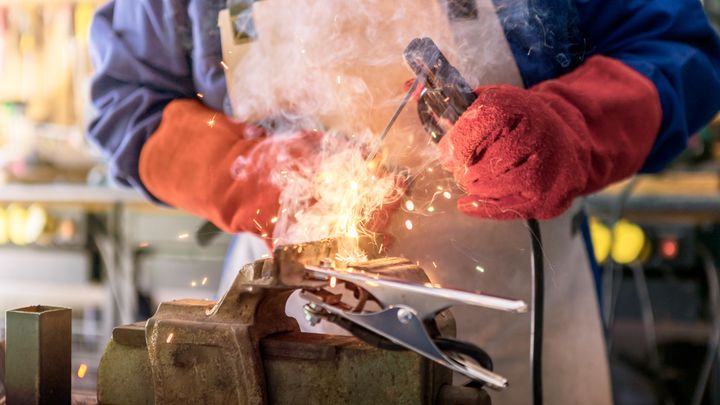
4. respiratory protection
To protect against the various fumes, gases and metal particulates that emanate from welding, welders should wear appropriate respiratory protection, such as air-purifying respirators or supplied-air respirators, depending on the specific welding process and the level of exposure.
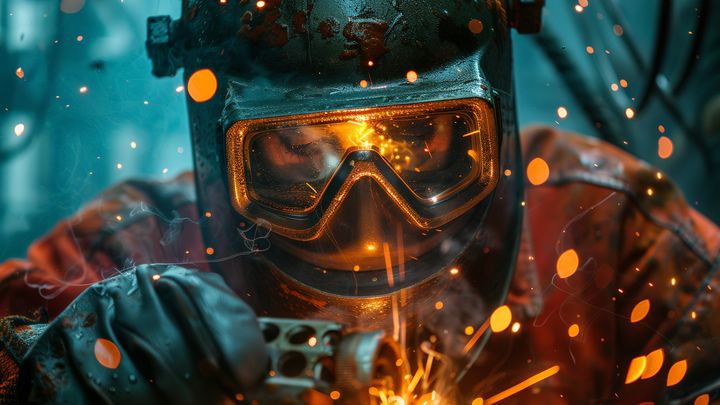
5. appropriate safety footwear
Welders should wear safety boots or shoes with non-slip soles and metatarsal guards to protect their feet from falling objects, molten metal splashes, and sharp debris. These shoes should also be heat-resistant and provide adequate insulation against electrical hazards.
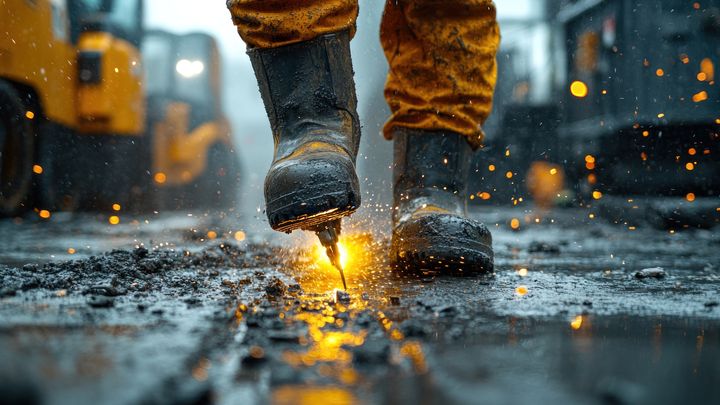
5. musculoskeletal disorders
Welding work often involves sitting and bending your neck and/or back into awkward postures, repetitive motions, and heavy lifting, which can lead to musculoskeletal disorders (MSDs) such as back pain, neck strain, carpal tunnel syndrome, and tendonitis. These injuries can be debilitating and may require time off work for recovery.
Unfortunately, ergonomic risks in welding arise from the nature of the work itself. Welders frequently have to bend, twist, and reach into confined spaces, putting strain on their backs, shoulders, and necks. Holding welding guns or torches for extended periods can cause hand, wrist, and arm fatigue. Plus, welders may need to lift and manoeuvre heavy materials, increasing the risk of back injuries.
prevention
Hope isn’t all lost, and there are lots of ways to prevent MSDs. Including:
- Providing adjustable workstations and welding booths that allow for comfortable postures and minimise reaching and bending.
- Using ergonomic tools and equipment, such as counterbalanced welding guns or torches, to reduce hand and arm strain.
- Implementing job rotation and frequent breaks to alleviate repetitive stress and fatigue.
- Training welders on proper lifting techniques and using mechanical aids for heavy loads.
- Encouraging stretching and warm-up exercises before, during (shifts) and after work.
Employers should also conduct ergonomic assessments to identify and mitigate specific MSD risks in their welding operations. Regular monitoring and adjustments to work practices can help prevent musculoskeletal injuries and ensure a safer and more productive welding workforce.
frequently asked questions about welding injuries and welding wearer protection
Welding PPE should be replaced the moment it shows signs of wear and tear or damage, or according to the manufacturer's recommendations. For example, welding helmets should be replaced if the lens is cracked or the helmet is damaged, and respirators should be replaced according to the filter's lifespan.
Welders can be at an increased risk of an illness called ‘metal fume fever’. People also call it ‘welder's cough’. Welders will typically feel sick 4 to 10 hours after they're exposed and might have flu-like symptoms such as a high temperature, shaking, sore joints, aching muscles, a headache, a cough, feeling sick to their stomach, and just feeling bad all over.
It’s important to take a break as soon as you notice symptoms and seek medical attention. It’s also worth assessing your PPE - particularly your respirator - to ensure it’s fit for purpose.
You need to take a shower after welding because the process creates metal dust, fumes, and other contaminants that can end up on your skin, hair, and clothes. These particles can be poisonous or cause irritation, leading to skin problems or breathing issues if you don't wash them off. Plus, some metals such as zinc or lead, can harm your health in the long run if your body absorbs them or you breathe them in. Taking a shower helps to get rid of these harmful particulates, which keeps them from touching your skin and lowers the chance of bringing dangerous materials home.
Looking for high-quality, comfortable welding PPE? Here at alsico, we design and supply specialist uniforms, protective and emergency response workwear - among a wide range of other industries and applications. Get in touch today to learn more about our product range or enquire about our bespoke design service.
learn more about the environments we supply into
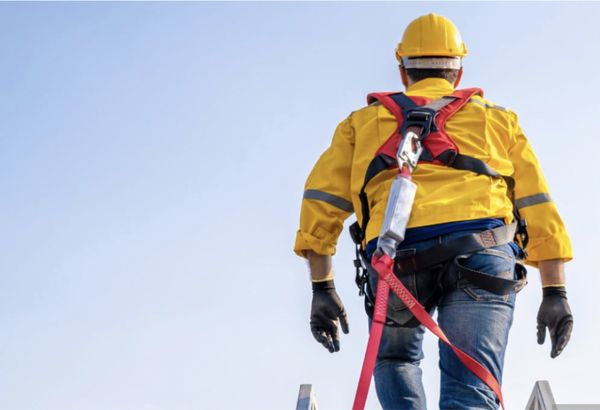
Environments
wearer protection
Protection is weaved into every part of alsico, we build it into everything we do and it drives our every decision. Our protective workwear range covers all high-safety sectors.
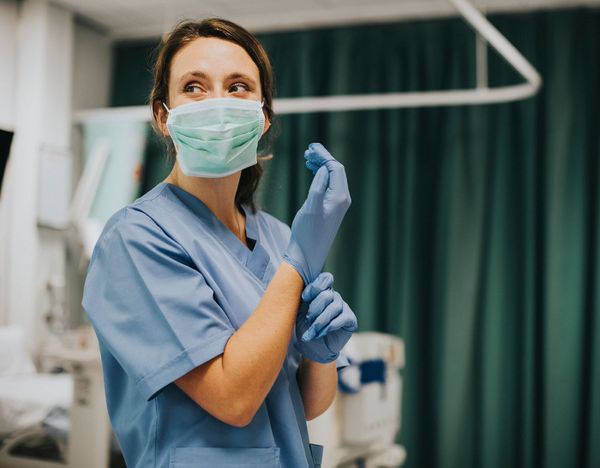
Environments
healthcare
We are one of the largest healthcare uniform suppliers in the UK, and are the majority supplier for the new NHS National Healthcare Uniform project.
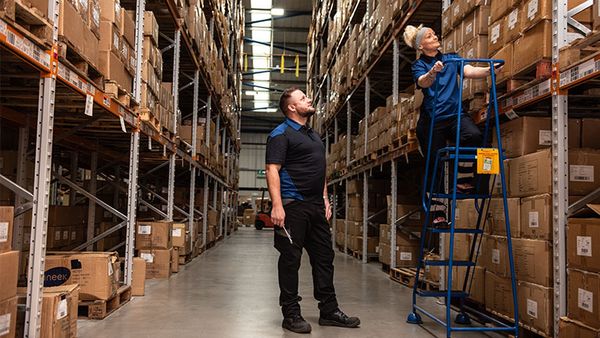
Environments
workwear
At alsico, we have shown excellence in a wide range of work uniforms, ranging from warehousing to global travel companies and from transportation to construction.
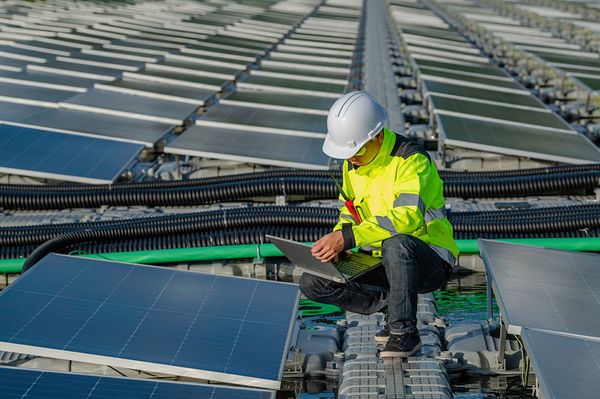
Environments
electrification
Our passion for creating innovative fabrics has positioned us as a key supplier in the exciting new sector of electrical safety clothing, from battery companies to aerospace, to all anti-static environments.
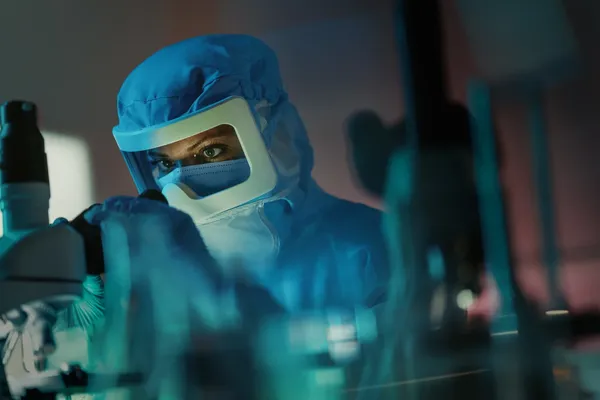
Environments
contamination control
We have developed a specialism in cleanroom clothing and uniforms, delivering exceptional performance in highly controlled environments.
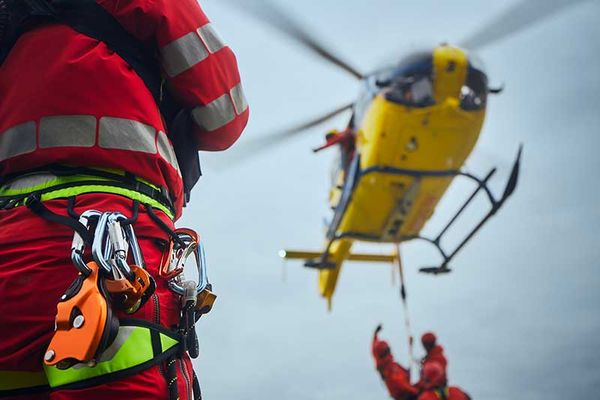
Environments
emergency response
We are always honored to be asked to provide workwear for our emergency services teams. We put our trust in them to help to look after us, and we do our very best in return, delivering performance when it matters.
contact us