1 April 2025
Common arc flash injuries and how to prevent them
Arc flashes are amongst the most dangerous electrical hazards in industrial environments, capable of causing severe injuries or even fatalities. These high-energy events can result from equipment failure, human error, or poor maintenance, releasing extreme heat, pressure, and radiation.
For those working in sectors like energy, construction, or railways, understanding the risks associated with arc flashes and knowing how to prevent them is critical for safety.
In this post, we'll explore the common causes of arc flashes, the injuries they can cause, and the essential steps you can take to prevent these incidents from occurring - including providing arc flash protective clothing. Whether you're an employer, safety manager, or electrical worker, being informed about arc flash safety is key to reducing the risk of devastating injuries on the job.
what is arc flash?
An arc flash is a sudden and intense release of energy caused by an electrical fault, such as a short circuit, that creates an electrical arc. It occurs when an electrical current jumps across an air gap between conductive materials.
This event is highly dangerous due to the immense energy release, which includes:
1. intense heat
Temperatures in an arc flash can reach up to 19,400°C, hotter than the surface of the sun. This heat can instantly vaporise metal and cause severe burns.
2. high pressure
The rapid expansion of air and vaporised metal creates a blast, which can knock workers off their feet or throw objects at high speeds.
3. bright light and radiation
The flash of light can cause temporary or permanent blindness, and the intense ultraviolet (UV) radiation can damage skin and eyes.
4. molten metal
The extreme heat can melt and vaporise surrounding materials, including copper, aluminium, or steel, turning them into molten droplets that can cause serious burns.
what can cause an arc flash?
Arc flashes can have a variety of different causes, so it’s important to understand how different causes can occur - to prevent them from happening. These include:
1. human error
Arc flashes can happen when a worker accidentally touches live electrical parts with tools or equipment. Mistakes during installation, maintenance, or repair tasks can also cause short circuits. Not adhering to proper safety practices, such as neglecting lockout/tagout procedures, also increases the likelihood of an arc flash.
2. equipment failure
Over time, electrical equipment can degrade, leading to insulation failure, loose connections, or exposed wires, which can result in an arc flash. Furthermore, malfunctioning switches, circuit breakers, or transformers may also fail to contain electrical arcs, especially under high-voltage conditions.
3. improper installation
Incorrect installation of electrical systems, such as improper grounding or phase conductors being too close to each other, can lead to short circuits that trigger an arc flash. Moreover, using the wrong type of components for specific voltage levels or environments increases the risk of equipment failure, which could result in an arc flash.
4. dust, corrosion, and contaminants
Dust, dirt, and other contaminants can build up on electrical equipment, creating conductive paths for electrical current to flow, leading to an arc. Rust and corrosion can also degrade electrical connections or insulation, increasing the likelihood of an arc flash incident.
5. overvoltage and faulty connections
Excessive current flowing through equipment beyond its designed capacity can cause insulation failure or short circuits that result in an arc flash. Additionally, improper or deteriorated connections between electrical components, such as loose bolts or damaged wires, can create the conditions for an arc flash.
6. exposure to moisture or condensation
Water or moisture entering electrical enclosures can create conductive paths between components, causing short circuits that can result in an arc flash. High-humidity environments increase this risk, as it can cause condensation inside electrical panels, increasing the risk of an arc flash due to the presence of moisture on live electrical parts.
7. voltage transients (surges or spikes)
Voltage spikes caused by lightning strikes, power fluctuations, or switching operations can stress electrical systems and lead to insulation failure or short circuits, triggering an arc flash.
8. insulation breakdown
Over time, insulation around conductors can degrade due to heat, exposure to chemicals, or mechanical wear, making it easier for electricity to arc between conductors. What’s more, using insulation that isn't rated for the system's voltage or environment can lead to breakdowns and arc flashes.
9. faulty circuit breakers or relays
Circuit breakers and protective relays that fail to operate correctly may not interrupt short circuits in time, leading to sustained faults that can cause an arc flash.
10. animals or foreign objects
Small animals, insects, or even tools accidentally left inside electrical cabinets can bridge live conductors, causing an arc flash.
common arc flash injuries
When an arc flash happens, it can cause serious injuries to all caught in the blast. Common arc flash injuries include:
1. thermal burns
Arc flashes produce extreme temperatures, leading to severe thermal skin burns. These burns can be fatal or require extensive medical treatment.
2. hearing loss
The sound produced by an arc flash can reach levels over 140 decibels, which is enough to cause permanent hearing damage. Victims may experience partial or complete hearing loss.
3. vision damage
The bright light and UV radiation from arc flashes can damage the eyes, causing flash burns or blindness. This can cause short- and long-term vision problems, including permanent blindness.
4. blast injuries
The explosive force from an arc flash can cause physical trauma including fractures and contusions. Injuries from being thrown or hit by debris can be as severe as direct electrical injuries, and even fatal injuries.
5. respiratory damage
Arc flashes can vaporise metal, releasing toxic fumes that can lead to respiratory problems if inhaled. This can lead to long-term respiratory illnesses, particularly for workers exposed repeatedly.
6. electrocution
Workers may experience electrical shocks during an arc flash. Direct contact with high-voltage currents can cause fatal electrocution.
how to prevent arc flash injuries
Preventing arc flash injuries involves a combination of proper training, safety practices, equipment maintenance, and personal protective equipment (PPE). Here are key methods to reduce the risk of arc flash incidents:
1. conduct hazard analysis
Perform an arc flash risk assessment to evaluate potential hazards. This includes calculating incident energy levels to determine the required protection for workers.
Then, mark electrical panels and equipment with labels that indicate the arc flash boundary, hazard levels, and required PPE.
2. de-energise equipment before work
Always de-energise equipment and follow proper LOTO procedures before performing maintenance or repair. This ensures that no accidental energising occurs whilst workers are handling electrical systems. Use appropriate testing tools to verify that the equipment is de-energised before starting work.
3. use of personal protective equipment (PPE)
Workers should wear arc flash protective clothing, including flame-resistant clothing, that is appropriate for the incident energy levels identified in the risk assessment, along with additional PPE such as arc-rated gloves, face shields, goggles, and dielectric footwear. Insulated tools should also be used to prevent accidental contact with live parts.
Ensure all PPE fits properly and is maintained according to the manufacturer’s recommendations to ensure protection during an arc flash event.
4. training and awareness
Provide workers with training on electrical safety standards. Workers should receive training specific to the electrical systems they will be working on, including how to recognise hazards, use PPE, and respond to arc flash incidents.
Who needs arc flash training?
Here’s a list to help you determine who needs arc flash training:
- Qualified electrical workers
- Unqualified workers who may be exposed to electrical hazards
- Supervisors and safety managers
- Facility owners and managers
- Construction and industrial workers
- Maintenance personnel
- Emergency responders
- Contractors and subcontractors
- Design and planning engineers
- Anyone involved in electrical safety audits or compliance
5. proper equipment maintenance
Periodically inspect electrical equipment for signs of wear, corrosion, or damage. Replace or repair damaged components promptly. You should also ensure that electrical systems are installed and maintained according to industry standards, to prevent faults that could lead to arc flash incidents.
6. safe work practices
Define and enforce arc flash boundaries (the distance within which PPE is required to protect against arc flash hazards). Ensure only qualified personnel enter these boundaries, and avoid working close to energised equipment if possible, or use remote operation to stay out of the arc flash boundary.
You should also use tools that are designed and rated for electrical work to minimise the risk of accidental contact with live parts.
7. plan for emergency response
Have an emergency action plan in place that includes procedures for treating arc flash injuries, such as burns or trauma, and rapid evacuation if necessary. Workers should also be trained in basic first aid for burns and other injuries caused by arc flash events.
8. install arc flash mitigation technology
Install arc flash protection relays, which detect arc faults and trip breakers or cut off power rapidly to reduce the energy of the arc flash, and current-limiting devices, which limit the fault current and reduce the incident energy during an arc flash, making the event less severe.
You should also ensure that the electrical system has proper grounding and ground fault protection to prevent arc flash incidents due to faults.
standards and regulations for arc flash safety
In the UK, arc flash safety is governed by a combination of national and international standards, regulations, and best practices. These standards aim to ensure that employers and workers take the necessary steps to prevent arc flash incidents and manage electrical hazards.
Here’s an overview of key standards and regulations relevant to arc flash safety in the UK:
1. electricity at work regulations 1989 (EWR)
The Electricity at Work Regulations 1989 is the primary regulation in the UK concerning electrical safety in the workplace. It requires employers to ensure that electrical systems are constructed, maintained, and operated in a way that prevents danger.
Relevant sections for arc flash safety include:
- Regulation 4: Ensures electrical systems are designed to prevent danger, which includes the risk of arc flash.
- Regulation 14: Specifies that no person should work on live conductors unless it is unreasonable to work without them being live and that suitable precautions, such as PPE, are taken.
- Regulation 16: Mandates appropriate training and competence for workers who may face electrical hazards.
2. BS EN 50110-1 (Operation of Electrical Installations)
This European Standard, adopted in the UK as BS EN 50110-1, sets out the safe operation of electrical installations, including maintenance, inspection, and procedures for working on or near live systems.
It covers requirements for risk assessments and ensuring electrical systems are properly managed and the use of personal protective equipment (PPE) and safe working distances to protect against electrical hazards like arc flashes.
3. BS 7671 (IET Wiring Regulations)
The IET Wiring Regulations (BS 7671), often referred to as the 17th Edition or 18th Edition, provide standards for the design, installation, and inspection of electrical installations in the UK. Whilst it primarily focuses on electrical design, it includes guidance for minimising risks that can lead to arc flashes, such as proper grounding, insulation, and the use of protective devices like circuit breakers.
4. Health and Safety at Work Act 1974 (HSWA)
The Health and Safety at Work Act (HSWA) 1974 is the overarching legislation that places a duty of care on employers to ensure the health, safety, and welfare of their employees.
For arc flash safety, this means that employers must assess electrical risks (including arc flash hazards) and implement controls to mitigate these risks. Section 2 and Section 3 emphasise the need for ensuring the safety of workers and anyone who might be affected by electrical work.
5. HSG85 (Electricity at Work: Safe Working Practices)
Electricity at Work: Safe Working Practices is published by the Health and Safety Executive (HSE) and provides practical guidance for complying with the Electricity at Work Regulations.
It includes specific advice on identifying and controlling risks associated with arc flash incidents, safe isolation procedures, risk assessments, and methods to prevent dangerous electrical conditions, and the use of appropriate PPE and safe work practices when working on or near live systems.
6. PPE Regulation (Personal Protective Equipment Regulations 2002)
PPE regulations ensure that employers provide arc-rated PPE to workers who may be exposed to arc flash hazards. The PPE must meet the required standards and protect against the risks identified in risk assessments. Employers must provide PPE that is suitable for the level of incident energy (calculated in the arc flash risk assessment) that workers might face.
7. ISO 45001 (Occupational Health and Safety Management Systems)
Whilst not specific to electrical safety, ISO 45001 is a globally recognised standard for health and safety management systems. It can be used to integrate arc flash safety measures into a company’s broader safety management practices.
By implementing ISO 45001, organisations can systematically manage arc flash hazards, ensuring risk assessments, training, and incident responses are part of their safety culture.
8. BS EN 61482 (Arc Flash PPE Standards)
BS EN 61482 provides standards for clothing and protective equipment designed to protect workers from arc flash injuries. It sets out testing procedures and performance requirements for arc-rated PPE.
- BS EN 61482-1-1: Describes testing using the open arc method to determine the Arc Thermal Performance Value (ATPV) of PPE.
- BS EN 61482-1-2: Uses the box test method, which simulates arc flash conditions in a confined space.
9. NFPA 70E (Standard for Electrical Safety in the Workplace)
Whilst primarily a U.S. standard, NFPA 70E is often referenced in the UK for guidance on arc flash safety. It provides comprehensive safety practices for electrical work, including arc flash risk assessment procedures, guidelines for selecting appropriate arc-rated PPE based on incident energy levels, and training requirements for workers exposed to electrical hazards.
Though NFPA 70E is not a legal requirement in the UK, many multinational companies and safety professionals use its detailed guidance as best practice.
10. IEC 61482-2 (Live working - Protective clothing against the thermal hazards of an electric arc)
IEC 61482-2 is a key international standard that outlines the requirements and testing methods for protective clothing against the thermal hazards of an electric arc, commonly known as arc flash protective clothing. This standard ensures that personal protective equipment (PPE), such as garments and materials, offers adequate protection for workers who may be exposed to arc flashes in electrical environments.
Arc flash protection from alsico
Alsico provides a comprehensive range of arc flash protective clothing, designed to shield workers from the dangers of arc flash incidents. Their garments, such as flame-resistant (FR) polo shirts, sweatshirts, and coveralls, are tailored to meet rigorous safety standards. These clothes are designed to prevent severe injuries by withstanding high heat and flames, making them essential in high-risk industries like energy, construction, and railway sectors.
Alsico's arc flash gear incorporates advanced materials like Modacrylic and Nomex®, ensuring not only fire resistance but also comfort and durability. These garments conform to EN safety standards (like IEC 61482-2 for arc protection), providing essential protection from thermal energy released during an arc flash.
In addition to arc flash protection, alsico's workwear also includes features like anti-static properties and high visibility to enhance overall safety. Our focus on innovation, including sustainable fabric solutions, ensures that wearer protection is both effective and environmentally conscious.
For reliable and customised arc flash protection, contact us today to learn more about our bespoke design and embroidery services. Whether you need flame-resistant clothing, arc-rated workwear, or protective gear for high-risk electrical environments, we offer both ready-made garments and tailor-made solutions to meet your specific safety requirements.
learn about the different environments of wearer protection we cater for
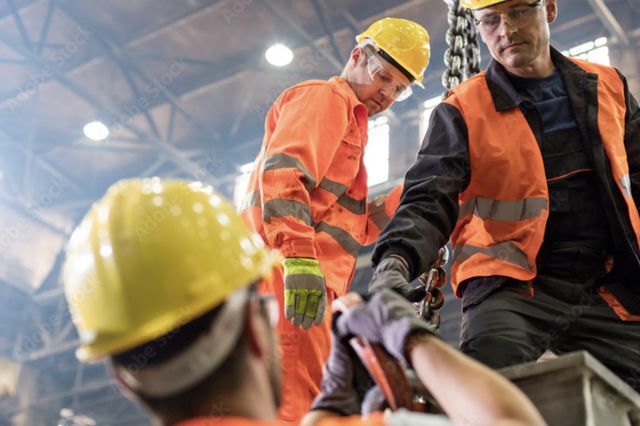
electricity and arc flash
Our clothing, tailored to specific risk levels, offers significant protection, enhancing safety in industries where Arc Flash incidents are prevalent, minimising the risk of serious burns and injuries.
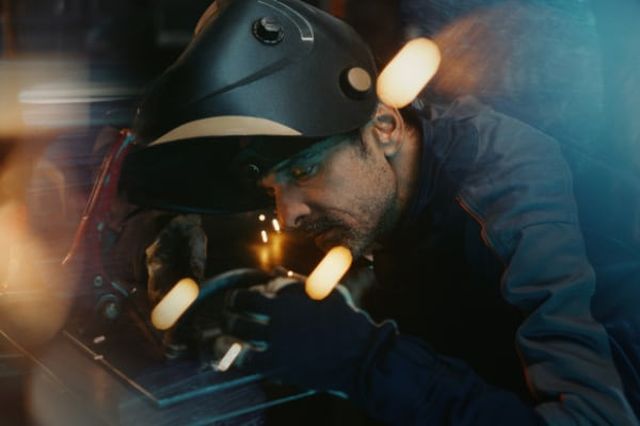
heat, flame, and welding
Burning hot embers, sparks and fire should never touch the skin of a human, our high-performance, FR and Welding protection garments are essential for workers in these environments.
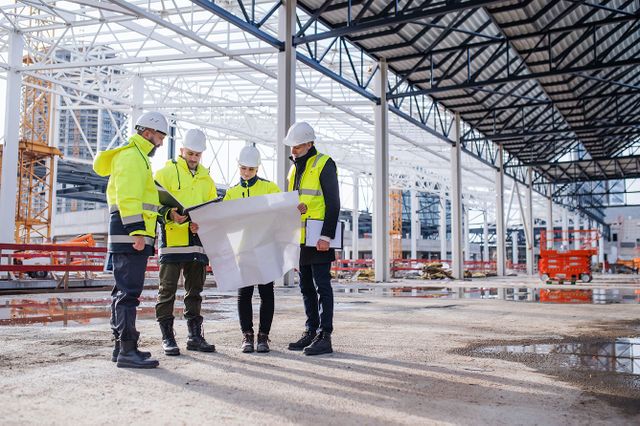
visibility
Stay seen and secure with our high-visibility solutions, designed to keep workers visible and protected in environments such as railways, roads, docks, airports, and construction.
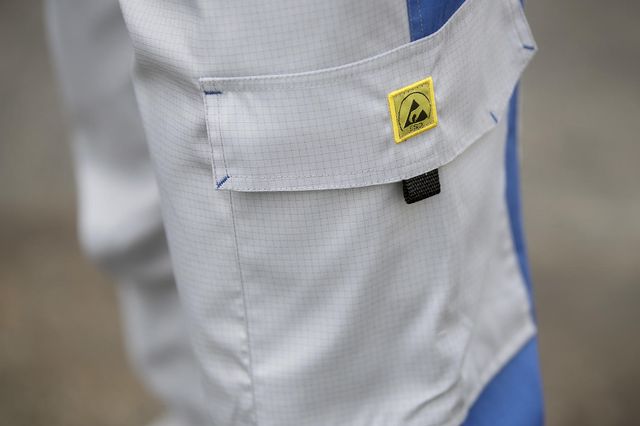
anti-static / ESD
Industries where electrostatic discharge poses a threat require anti-static/ESD garments. These specialized garments prevent static electricity buildup during sensitive operations, providing a crucial line of defense for worker safety.
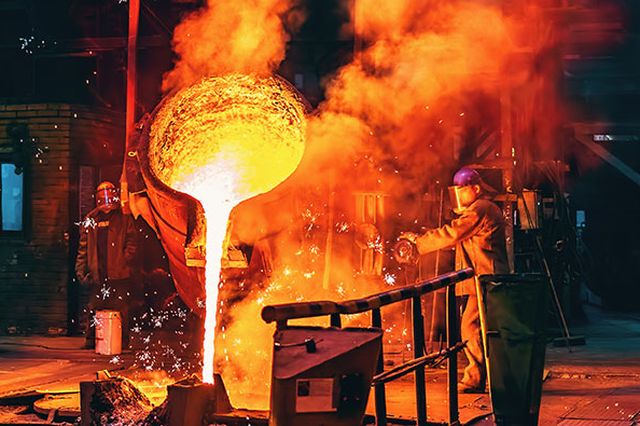
molten metals
Protective solutions to ensure your team's safety from molten metal hazards, ensuring maximum-level protection against various metals, including zinc, nickel, and lead, ensuring your team's safety.
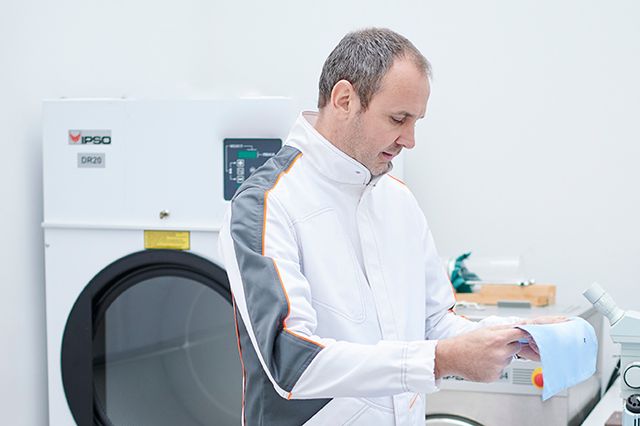
chemical
Chemical-resistant attire is necessary for protecting workers from hazardous substances in various industries. Alsico's reliable protective clothing creates a secure barrier against potentially harmful chemicals, prioritizing workplace safety.
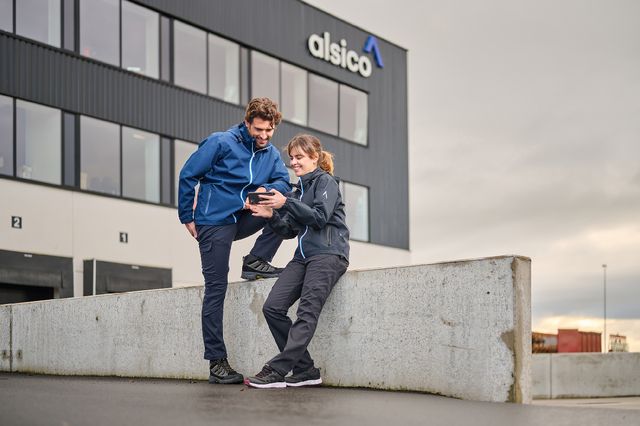
rain and cold
Rain and cold weather workwear is pivotal in ensuring safety and comfort in challenging conditions, ensuring workers across diverse industries can perform their tasks safely and efficiently.
contact us